SINGLE-PLY
Single-Ply Roofing has grown tremendously in popularity over the past several decades and has become the roofing of choice for commercial contractors. When properly installed, Single-Ply roofs offer many advantages such as the following:
- Strength
- Excellent reflective properties
- Resistance to acid rain and other chemical pollutants
- Very lightweight
- Excellent performance in extreme weather
- Comparatively low cost
Types and Uses
Formed from compounded, plastic-derived material into flexible sheets, Single-Ply roofing is typically used to cover flat and low-sloped buildings. The three main types of Single-Ply roofs are PVC (Polyvinyl Chloride), TPO (Thermoplastic Polyolefin) and EPDM (Ethylene Propylene Diene Monomer).
Installation Methods
The methods of Single-Ply roofing installation Martin roofing typically uses are as follows:
A ballasted system uses large panels of rubber membrane, typically 50-200 feet in size, loose-laid atop the roofing insulation, and then covered with ballast, such as river stone. This is a lower-cost option providing rapid coverage.
A fully adhered system is ideal for roofs with a slight slope. Mounting plates anchor roofing insulation to the roof deck. The Single-Ply roofing is then bonded to the insulation.
Systems using mechanical attachment first affix mounting plates to the roof deck through the roofing insulation. Next, the membrane is placed and attached to the underlying plates.
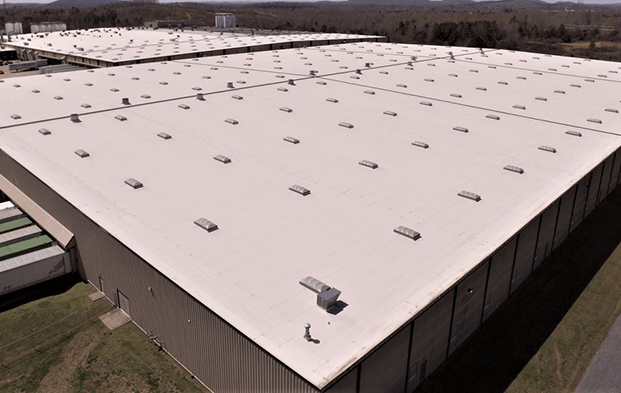